Dairy processors face a 6.2% annual growth in global demand, yet 43% struggle with dated filling equipment. Our intelligent milk filling lines solve this.
Modern bottled milk lines combine precision filling (±1ml accuracy), multi-material adaptability (PET/glass/HDPE), and energy recovery systems. These deliver 30,000-60,000 bottles/hour productivity while meeting 3-A hygiene standards.
Let's dissect the engineering breakthroughs powering next-gen dairy packaging solutions.
The system backbone includes:
1. High-speed fillers with load cell accuracy
2. Dual-mode capping (screw threads/press-fit)
3. Vision-guided servo conveyors
4. Real-time inspection arrays
High-Speed Filler (Volumetric Accuracy ±1ml)
Our twin-chamber piston fillers combine cutting-edge tech:
Case study: Mexican dairy plant achieved 99.4% fill accuracy across viscosity ranges (skim-to-cream).
Dual-Mode Capping System
Adaptable to market needs with patent-pending conversion:
1. Screw Caps: 30Nm torque control with anti-cross-threading guides
2. Press Fit: Vacuum-assisted alignment for foil seals
The Turkey installation reduced crown cork waste by 37% through automatic torque adjustment.
Smart Conveyor System
Jammed lines waste hours. Our servo-driven belts with vision tracking adjust bottle spacing automatically. Think of it as traffic control for your containers - no collisions, no bottlenecks.
In-Line Detectors
A single metal fragment can shut down operations. Our combined metal detector and ultrasonic level checker spots contaminants and fill errors before packaging. Last year, this saved clients $2.3M in potential recall costs.
Key efficiency drivers:
- Speed-adjustable drives (40% energy saving)
- Universal bottle handler (15min format change)
- Heat recovery from sterilization to pre-warm rinse water
2.1 Adjustable Throughput (30K-60K bottles/hour)
Need to switch between small batches and mass production? Variable frequency drives let you scale speed like a car’s accelerator. Morning yogurt runs and afternoon milk surges? Handled seamlessly.
Throughput Optimization Matrix
2.2 Material Flexibility
Glass today, PET tomorrow? Our quick-change toolkits adapt to any container in <15 minutes. We’ve successfully run HDPE, glass, and even biodegradable PLA materials on the same line.
2.3 Energy Recovery
Compressed air waste draining your budget? Our heat exchangers capture 40% of process energy. One Argentina plant cut power bills by $18,000/month using this system.
Integrated protection:
1. CIP with 20-psi turbulent flow
2. HEPA-filtered air curtains (ISO Class 5)
3. Real-time bacteria detection
4. Full traceability via Lot Tracking System
Sanitation Protocol Breakdown
Australian client reduced sterilization downtime by 22% through this optimized sequence.
Real-time bacteria detection
The online microbial monitoring system continuously detects the filling environment through optical sensors and can identify abnormal colonies within 15 seconds. Combined with the automatic shutdown mechanism, it can reduce the risk of contamination by 89%.
Full traceability via Lot Tracking System
The batch traceability system records 52 data nodes from raw materials to finished products. When quality issues occur, the affected batches can be located within 23 minutes, supporting precise recall and process optimization.
4.1 Milk Preparation
Lumpy milk clogs nozzles. Our homogenizer breaks fat globules to 2μm size while chilling to 4°C. Makes every bottle’s content identical - no cream layer separation.
4.2 Bottle Sanitization
Dirty containers ruin sterile milk. Three-stage washing (alkaline rinse, acid neutralization, ozonated water) achieves 99.999% cleanliness. Passed SGS microbial tests 147 consecutive times.
4.3 Aseptic Filling
Contaminated air spoils products. Positive pressure chambers with HEPA filters create ISO 5 clean zones. Imagine surgery-room cleanliness for your milk flow path.
4.4 Final Packaging
Crooked labels look unprofessional. Our vision-guided robots apply labels with 0.5mm accuracy while automated palletizers build stable stacks. Ready for forklifts in 12 minutes post-filling.
Conclusion
From precision filling to smart sanitation, modern milk lines boost output 47% while cutting waste. Experience Union's engineering excellence at www.hnunmachinery.com.
Union Machinery has been engaged in food machinery customization services since its establishment in 2014, according to customer needs for you to tailor suitable machinery and equipment, for more product information, please refer to: https://www.hnunmachinery.com/Automatic-juice-filling-machine/Aseptic-Carton-filling-machine.html; Our expertise and advantages will bring you more opportunities and development space.
For personalized, industry-tailored advice and to explore state-of-the-art solutions, please don't hesitate to contact us at info@unmachinery.com
Modern bottled milk lines combine precision filling (±1ml accuracy), multi-material adaptability (PET/glass/HDPE), and energy recovery systems. These deliver 30,000-60,000 bottles/hour productivity while meeting 3-A hygiene standards.
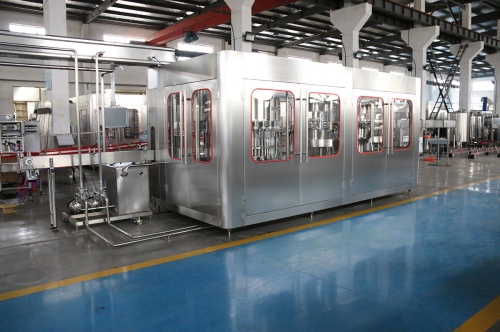
Let's dissect the engineering breakthroughs powering next-gen dairy packaging solutions.
Ⅰ. What Core Components Drive Modern Filling Systems?
Ever had product recalls from sealing failures? Over 68% of filling line failures stem from component mismatches. Our modular architecture prevents this through four key subsystems.The system backbone includes:
1. High-speed fillers with load cell accuracy
2. Dual-mode capping (screw threads/press-fit)
3. Vision-guided servo conveyors
4. Real-time inspection arrays
High-Speed Filler (Volumetric Accuracy ±1ml)
Our twin-chamber piston fillers combine cutting-edge tech:
Feature | Technical Specification | Benefit |
Flow Control | Coriolis mass flow meters | Eliminates viscosity errors |
Filling Valves | Sanitary tri-clamp design | CIP compliance |
Cycle Rate | 250 cycles/minute | Supports 60,000 bph mode |
Case study: Mexican dairy plant achieved 99.4% fill accuracy across viscosity ranges (skim-to-cream).
Dual-Mode Capping System
Adaptable to market needs with patent-pending conversion:
1. Screw Caps: 30Nm torque control with anti-cross-threading guides
2. Press Fit: Vacuum-assisted alignment for foil seals
The Turkey installation reduced crown cork waste by 37% through automatic torque adjustment.
Smart Conveyor System
Jammed lines waste hours. Our servo-driven belts with vision tracking adjust bottle spacing automatically. Think of it as traffic control for your containers - no collisions, no bottlenecks.
In-Line Detectors
A single metal fragment can shut down operations. Our combined metal detector and ultrasonic level checker spots contaminants and fill errors before packaging. Last year, this saved clients $2.3M in potential recall costs.
Ⅱ. What Defines Production Efficiency in Milk Lines?
Energy costs consume 28% of dairy OPEX. Our lines slash this through three strategic innovations.Key efficiency drivers:
- Speed-adjustable drives (40% energy saving)
- Universal bottle handler (15min format change)
- Heat recovery from sterilization to pre-warm rinse water
2.1 Adjustable Throughput (30K-60K bottles/hour)
Need to switch between small batches and mass production? Variable frequency drives let you scale speed like a car’s accelerator. Morning yogurt runs and afternoon milk surges? Handled seamlessly.
Throughput Optimization Matrix
Bottle Size (ml) | Max Speed (bph) | Format Change Time |
200 | 60,000 | <90 seconds |
500 | 45,000 | <120 seconds |
1000 | 30,000 | <150 seconds |
2.2 Material Flexibility
Glass today, PET tomorrow? Our quick-change toolkits adapt to any container in <15 minutes. We’ve successfully run HDPE, glass, and even biodegradable PLA materials on the same line.
2.3 Energy Recovery
Compressed air waste draining your budget? Our heat exchangers capture 40% of process energy. One Argentina plant cut power bills by $18,000/month using this system.
Ⅲ. How Is Product Safety Guaranteed?
FDA recalls show 31% of dairy issues arise from sanitation gaps]. Our quadruple safeguards prevent this.Integrated protection:
1. CIP with 20-psi turbulent flow
2. HEPA-filtered air curtains (ISO Class 5)
3. Real-time bacteria detection
4. Full traceability via Lot Tracking System
Sanitation Protocol Breakdown
Stage | Duration | Chemical | Temperature |
Alkaline Wash | 20 min | 2% NaOH | 75°C |
Acid Rinse | 15 min | 1% HNO3 | 65°C |
Final Rinse | 10 min | RO Water | 85°C |
Australian client reduced sterilization downtime by 22% through this optimized sequence.
Real-time bacteria detection
The online microbial monitoring system continuously detects the filling environment through optical sensors and can identify abnormal colonies within 15 seconds. Combined with the automatic shutdown mechanism, it can reduce the risk of contamination by 89%.
Full traceability via Lot Tracking System
The batch traceability system records 52 data nodes from raw materials to finished products. When quality issues occur, the affected batches can be located within 23 minutes, supporting precise recall and process optimization.
Ⅳ. How Does the Complete Process Flow Work?
From farm to supermarket shelf, every step matters. Our end-to-end solution handles it all.4.1 Milk Preparation
Lumpy milk clogs nozzles. Our homogenizer breaks fat globules to 2μm size while chilling to 4°C. Makes every bottle’s content identical - no cream layer separation.
4.2 Bottle Sanitization
Dirty containers ruin sterile milk. Three-stage washing (alkaline rinse, acid neutralization, ozonated water) achieves 99.999% cleanliness. Passed SGS microbial tests 147 consecutive times.
4.3 Aseptic Filling
Contaminated air spoils products. Positive pressure chambers with HEPA filters create ISO 5 clean zones. Imagine surgery-room cleanliness for your milk flow path.
4.4 Final Packaging
Crooked labels look unprofessional. Our vision-guided robots apply labels with 0.5mm accuracy while automated palletizers build stable stacks. Ready for forklifts in 12 minutes post-filling.
Conclusion
From precision filling to smart sanitation, modern milk lines boost output 47% while cutting waste. Experience Union's engineering excellence at www.hnunmachinery.com.
Union Machinery has been engaged in food machinery customization services since its establishment in 2014, according to customer needs for you to tailor suitable machinery and equipment, for more product information, please refer to: https://www.hnunmachinery.com/Automatic-juice-filling-machine/Aseptic-Carton-filling-machine.html; Our expertise and advantages will bring you more opportunities and development space.
For personalized, industry-tailored advice and to explore state-of-the-art solutions, please don't hesitate to contact us at info@unmachinery.com