Jelly, as a widely popular dessert, involves a complex and precise production process. To ensure efficient, hygienic, and consistent production, modern jelly filling production lines have become indispensable. This article will take you through the detailed process of a jelly filling production line, step by step, from raw material preparation to finished product packaging, unveiling the mystery behind jelly production.
- Weighing and Proportioning: Precisely measure water, sugar, pectin, acidulants, flavors, and colorants according to the recipe.
- Mixing and Dissolving: Add the raw materials into a mixing tank, and heat and stir them to fully dissolve, forming a uniform jelly liquid.
- Filtration: Remove impurities from the jelly liquid to ensure the texture and appearance of the final product.
Key Equipment: Mixing tank, heating system, filtration device
- High-Temperature Sterilization: Heat the jelly liquid to 85°C–95°C to kill microorganisms(in line with the HACCP standards in Europe and America).
- Rapid Cooling: Quickly cool the jelly liquid to the filling temperature (usually 25°C–30°C) using a cooling system to prevent over-solidification.
Key Equipment: Plate heat exchanger, cooling tower
- Cup Feeding: Empty cups are neatly arranged and transported to the filling station via an automatic cup feeding system.
- Precise Filling: The jelly liquid is injected into the cups through filling nozzles according to the preset volume. For multi-layer jelly (e.g., jelly + fruit pieces), the equipment sequentially fills different components.
- Filling Accuracy Control: Modern fillers use high-precision sensors and control systems to ensure filling accuracy within ±1%.
Key Equipment: Automatic cup feeding system, filling machine, dosing pump
- Film Feeding: The sealing film is automatically fed and placed over the cup openings.
- Heat Sealing: The film is securely sealed to the cup through heating and pressure.
- Date Printing: Print production dates, expiration dates, and other information on the sealing film.
Key Equipment: Sealing machine, heat sealing device, date printer
- Cooling Tunnel: The jelly cups pass through a cooling tunnel, where the temperature gradually decreases, and the jelly liquid begins to solidify.
- Solidification Time Control: Adjust cooling time and temperature based on the jelly recipe and cup size to ensure complete solidification and uniform texture.
Key Equipment: Cooling tunnel, temperature control system
- Weight Check: Verify that the weight of each jelly cup meets the standard.
- Seal Check: Ensure the seal is intact and leak-free.
- Visual Inspection: Use cameras to check for defects (e.g., bubbles, impurities) in the jelly cups.
- Automatic Rejection: Automatically remove defective products from the production line.
Key Equipment: Weight checker, vision inspection system, automatic rejection device
- Automatic Packaging: The jelly cups are packed into cartons or plastic bags via a packaging machine.
- Boxing and Palletizing: The packaged jelly boxes are automatically loaded into cartons and neatly stacked on pallets by a palletizing robot.
- Labeling and Information Recording: Labels are applied to the cartons, and production batch information is recorded for traceability. it supports multi - language label printing (English/Arabic/Spanish, etc.), meeting the needs of cross - border logistics.
Key Equipment: Automatic packaging machine, boxing machine, palletizing robot
- CIP Cleaning System: Automatically clean filling nozzles, pipelines, and storage tanks to ensure hygiene.
- Equipment Maintenance: Regularly inspect and replace wear-prone parts to ensure long-term stable operation.
Key Equipment: CIP cleaning system, maintenance tools
- Consistent Quality: Precise control systems ensure consistent texture and appearance of each jelly cup.
- Food Safety: Complies with international hygiene standards, ensuring consumer health.
- Flexibility: Supports multiple cup types, recipes, and packaging formats to meet market demands.
✅ Customized Design: Adjust parameters according to the target market (for example, Middle Eastern clients require high - temperature - resistant filling heads, and American clients need NSF - certified models).
✅ High Efficiency and Reliability: Production capacity of over 10,000 cups per hour with stable operation.
✅ Global Certifications: Complies with FDA, CE, and other international standards, suitable for export markets.
✅ Comprehensive Support: Focusing on the export of food machinery for 11 years, serving customers from 58 countries. One-stop service from equipment selection to after-sales maintenance.
- For Southeast Asian/African clients: A cost - effective semi - automatic line (with a daily production capacity of 5 - 10 tons), suitable for environments with unstable power supply.
- For European and American clients: A fully - automatic line + AI quality control system, reducing human contact and passing the BRCGS certification.
Get a free solution: Click the send button below with your target production capacity/market, and we will send you a production line layout diagram + investment return calculation table within 48 hours.
Video factory inspection: Appointment engineer video factory inspection (360°real-time view of workshop and delivered equipment operation status)
Union Machinery has been engaged in food machinery customization services since its establishment in 2014, according to customer needs for you to tailor suitable machinery and equipment, for more product information, please refer to: https://www.hnunmachinery.com/Automatic-Cups-Filling-and-Sealing-Machine/More video information see view: cups-filling-and-foil-sealing-machine cups-filling-and-sealing-machine coffee-capsule-filling-and-sealing-machine;Our expertise and advantages will bring you more opportunities and development space.
For personalized, industry-tailored advice and to explore state-of-the-art solutions, please don't hesitate to contact us at info@unmachinery.com
The following is other knowledge related to the cups filling and sealing machine that I have summarized based on long-term work experience, for your reference. I hope it will be helpful to you.
1.What is the cup filling machine?
2.How to Choose the Perfect Jelly Filling and Sealing Machine?
3.What are the common faults of jelly filling and sealing machine?
4.How much does a jelly filling production line cost?
5.What is a cup yogurt filling and sealing machine?
6.How much is the cup yogurt filling and sealing machine?
1. Raw Material Preparation and Mixing
The starting point of jelly production is high-quality raw materials. This stage includes:- Weighing and Proportioning: Precisely measure water, sugar, pectin, acidulants, flavors, and colorants according to the recipe.
- Mixing and Dissolving: Add the raw materials into a mixing tank, and heat and stir them to fully dissolve, forming a uniform jelly liquid.
- Filtration: Remove impurities from the jelly liquid to ensure the texture and appearance of the final product.
Key Equipment: Mixing tank, heating system, filtration device
2. Sterilization and Cooling
To ensure food safety and extend shelf life, the jelly liquid undergoes sterilization:- High-Temperature Sterilization: Heat the jelly liquid to 85°C–95°C to kill microorganisms(in line with the HACCP standards in Europe and America).
- Rapid Cooling: Quickly cool the jelly liquid to the filling temperature (usually 25°C–30°C) using a cooling system to prevent over-solidification.
Key Equipment: Plate heat exchanger, cooling tower
3. Filling
Filling is the core stage of the jelly production line, directly affecting the product's appearance and consistency:- Cup Feeding: Empty cups are neatly arranged and transported to the filling station via an automatic cup feeding system.
- Precise Filling: The jelly liquid is injected into the cups through filling nozzles according to the preset volume. For multi-layer jelly (e.g., jelly + fruit pieces), the equipment sequentially fills different components.
- Filling Accuracy Control: Modern fillers use high-precision sensors and control systems to ensure filling accuracy within ±1%.
Key Equipment: Automatic cup feeding system, filling machine, dosing pump
4. Sealing
After filling, the jelly cups need to be immediately sealed to prevent contamination and leakage:- Film Feeding: The sealing film is automatically fed and placed over the cup openings.
- Heat Sealing: The film is securely sealed to the cup through heating and pressure.
- Date Printing: Print production dates, expiration dates, and other information on the sealing film.
Key Equipment: Sealing machine, heat sealing device, date printer
5. Cooling and Solidification
The sealed jelly cups undergo cooling and solidification:- Cooling Tunnel: The jelly cups pass through a cooling tunnel, where the temperature gradually decreases, and the jelly liquid begins to solidify.
- Solidification Time Control: Adjust cooling time and temperature based on the jelly recipe and cup size to ensure complete solidification and uniform texture.
Key Equipment: Cooling tunnel, temperature control system
6. Inspection and Rejection
To ensure the quality of each jelly cup, the production line conducts multiple inspections:- Weight Check: Verify that the weight of each jelly cup meets the standard.
- Seal Check: Ensure the seal is intact and leak-free.
- Visual Inspection: Use cameras to check for defects (e.g., bubbles, impurities) in the jelly cups.
- Automatic Rejection: Automatically remove defective products from the production line.
Key Equipment: Weight checker, vision inspection system, automatic rejection device
7. Packaging and Palletizing
The final step is packaging the finished jelly products and preparing them for shipment:- Automatic Packaging: The jelly cups are packed into cartons or plastic bags via a packaging machine.
- Boxing and Palletizing: The packaged jelly boxes are automatically loaded into cartons and neatly stacked on pallets by a palletizing robot.
- Labeling and Information Recording: Labels are applied to the cartons, and production batch information is recorded for traceability. it supports multi - language label printing (English/Arabic/Spanish, etc.), meeting the needs of cross - border logistics.
Key Equipment: Automatic packaging machine, boxing machine, palletizing robot
8. Cleaning and Maintenance
After production, the production line requires thorough cleaning and maintenance:- CIP Cleaning System: Automatically clean filling nozzles, pipelines, and storage tanks to ensure hygiene.
- Equipment Maintenance: Regularly inspect and replace wear-prone parts to ensure long-term stable operation.
Key Equipment: CIP cleaning system, maintenance tools
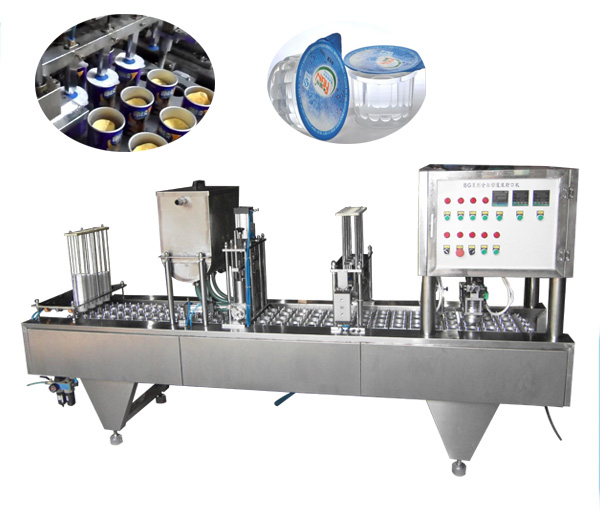
Advantages of Jelly Filling Production Lines
- High Efficiency: Automated equipment significantly improves production efficiency and reduces labor costs.- Consistent Quality: Precise control systems ensure consistent texture and appearance of each jelly cup.
- Food Safety: Complies with international hygiene standards, ensuring consumer health.
- Flexibility: Supports multiple cup types, recipes, and packaging formats to meet market demands.
Why Choose Union Machinery's Jelly Filling Production Line?
At Union Machinery, we provide customized, high-performance jelly filling production lines to help you achieve efficient, safe, and flexible production. Our equipment offers:✅ Customized Design: Adjust parameters according to the target market (for example, Middle Eastern clients require high - temperature - resistant filling heads, and American clients need NSF - certified models).
✅ High Efficiency and Reliability: Production capacity of over 10,000 cups per hour with stable operation.
✅ Global Certifications: Complies with FDA, CE, and other international standards, suitable for export markets.
✅ Comprehensive Support: Focusing on the export of food machinery for 11 years, serving customers from 58 countries. One-stop service from equipment selection to after-sales maintenance.
Your Exclusive Solutions
For different market pain points, we offer:- For Southeast Asian/African clients: A cost - effective semi - automatic line (with a daily production capacity of 5 - 10 tons), suitable for environments with unstable power supply.
- For European and American clients: A fully - automatic line + AI quality control system, reducing human contact and passing the BRCGS certification.
Want a production line that boosts your export competitiveness?


Union Machinery has been engaged in food machinery customization services since its establishment in 2014, according to customer needs for you to tailor suitable machinery and equipment, for more product information, please refer to: https://www.hnunmachinery.com/Automatic-Cups-Filling-and-Sealing-Machine/More video information see view: cups-filling-and-foil-sealing-machine cups-filling-and-sealing-machine coffee-capsule-filling-and-sealing-machine;Our expertise and advantages will bring you more opportunities and development space.
For personalized, industry-tailored advice and to explore state-of-the-art solutions, please don't hesitate to contact us at info@unmachinery.com
The following is other knowledge related to the cups filling and sealing machine that I have summarized based on long-term work experience, for your reference. I hope it will be helpful to you.
1.What is the cup filling machine?
2.How to Choose the Perfect Jelly Filling and Sealing Machine?
3.What are the common faults of jelly filling and sealing machine?
4.How much does a jelly filling production line cost?
5.What is a cup yogurt filling and sealing machine?
6.How much is the cup yogurt filling and sealing machine?