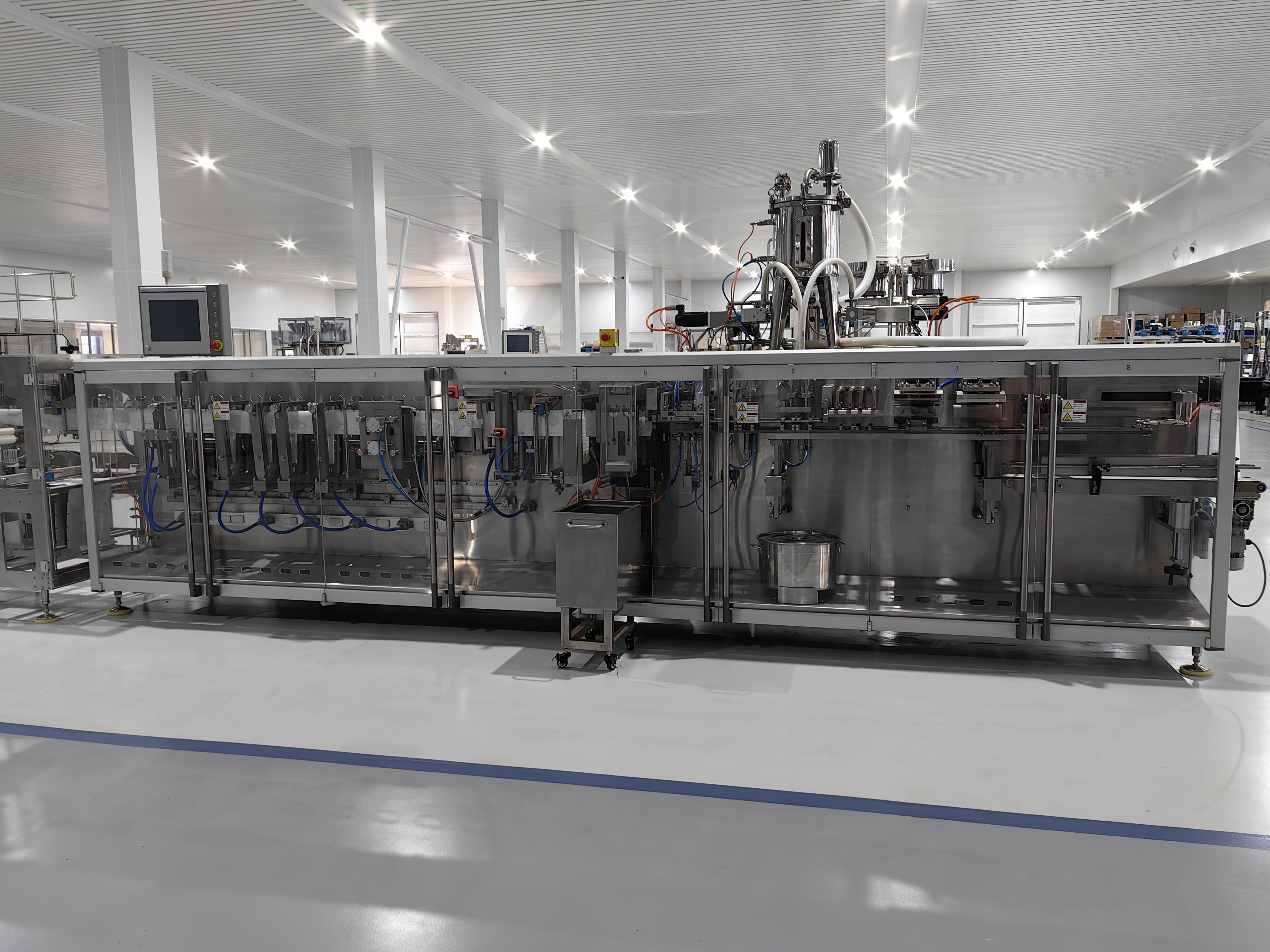
Choosing a suitable roll film horizontal packaging machine is crucial for improving production efficiency and product quality. How to choose a good film packaging machine? Careful consideration can be made from the following aspects:
1. Evaluate production capacity demand:
- Firstly, clarify your production scale and target output. The more expensive the price, the better. Choosing a packaging machine that matches your production capacity in terms of speed and size is the most cost-effective option.
- Consider the demand during peak hours to ensure that machines can continuously meet production requirements.
2. Understand product features:
Analyze the type of product you want to package (solid, liquid, powder, granule), packaging bag type (three sided seal, four sided seal, stand-up pouch, suction nozzle bag, zipper bag), size, weight, and packaging requirements (such as moisture resistance, gas resistance, transparency). Different products may require specific types of films and packaging methods, so choose a packaging machine that matches the product requirements.3. Investigate machine performance:
- Structural stability: Observing the overall structure and welding points of the fuselage, high-quality equipment usually has a stable frame without obvious deformation, cracks, or looseness, and can withstand long-term high-intensity operations without instability.
- Processing accuracy: Check the assembly accuracy of various moving parts, such as guide rails, rollers, cutters, etc. High accuracy means smoother operation and lower wear rate.
- Quality of parts: metal parts shall be made of anti-corrosion and wear-resistant alloy steel or stainless steel, and plastic parts shall have high toughness and anti-aging characteristics to ensure the durability of the whole equipment.
- Control system: Advanced PLC controllers and human-computer interaction interfaces should be responsive, easy to operate, support parameter setting and fault diagnosis, improve production efficiency and maintenance convenience.
- Packaging effect: The finished product packaging is tight and flat, with tight sealing, no signs of leakage, and a uniform shape, indicating high packaging accuracy of the equipment.
- Energy efficiency: The equipment should be equipped with an efficient and energy-saving power system to reduce power consumption and heat loss, and be low-carbon and environmentally friendly.
- Noise level: Under operating conditions, high-quality equipment produces less noise, indicating a reasonable internal structural design, smooth transmission, and reduced work pressure for operators.
- Usability and maintenance cost: Consider the user friendliness of the interface, as well as the convenience of daily cleaning and maintenance. The easy-to-use control panel and modular design facilitate quick learning and maintenance.
- Service life of vulnerable parts: Components that frequently come into contact with materials such as sealing strips, cutters, and belts should be wear-resistant, corrosion-resistant, and durable, reducing replacement frequency and maintenance costs.
- Safety protection: Multiple safety devices such as emergency stop buttons, safety doors, and photoelectric protection should be installed to ensure that operators can quickly evacuate in case of emergencies.
- Compatibility and Scalability: Ensure that new machines can integrate with existing production lines and have the potential to add additional functionality in the future for upgrading as business grows.
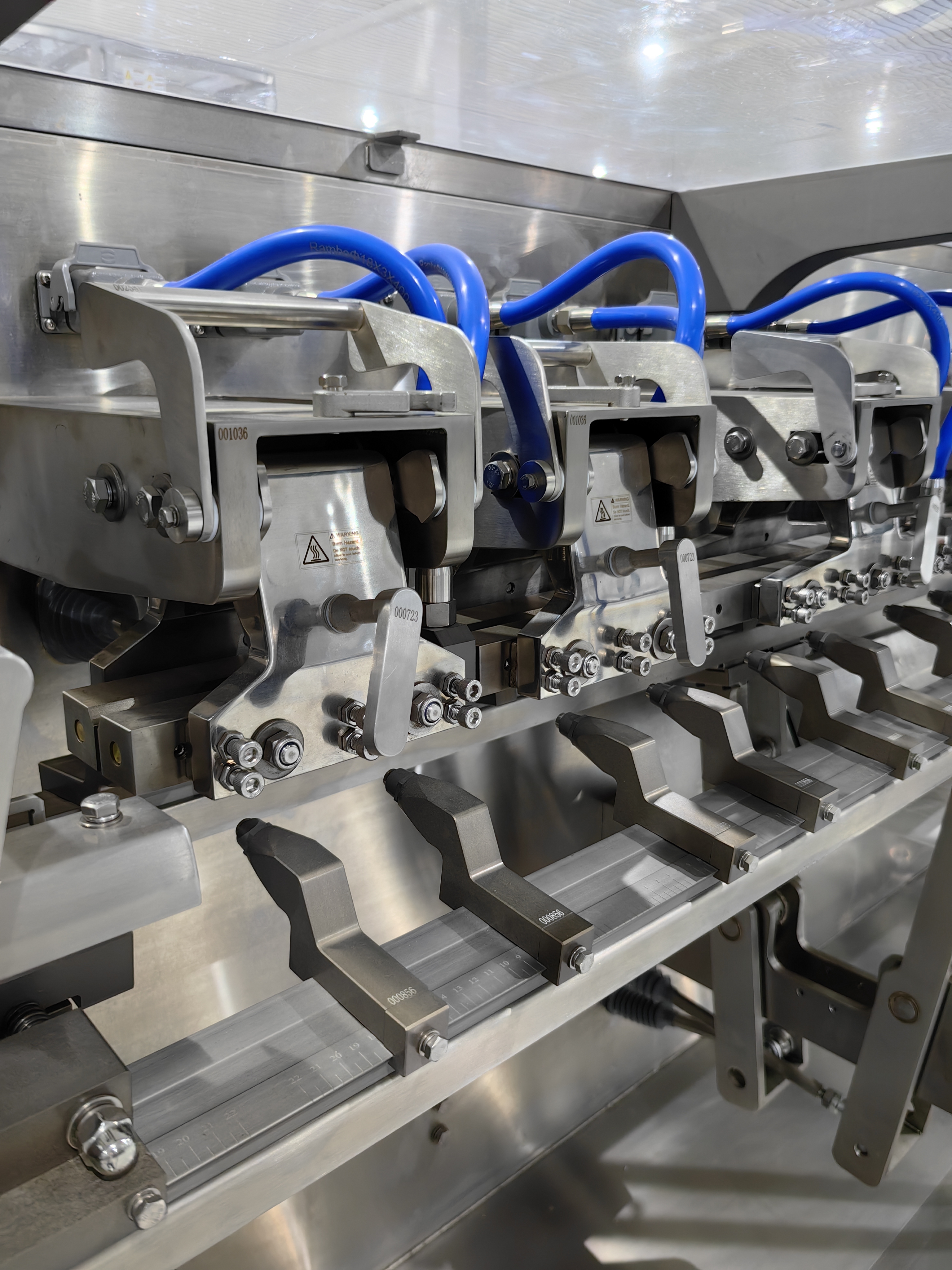
4. Budget evaluation:
Taking into account the purchase cost, energy consumption, labor, and maintenance expenses, calculate the total cost of ownership (TCO) and find the most cost-effective solution.5. Service and Support:
- Personnel training: Understand whether the supplier provides installation guidance, operational training, and technical support services to ensure a smooth transition and long-term support.
- After sales service: A comprehensive pre-sales consultation and after-sales service system, including equipment debugging, technical training, and regular maintenance plans, can better reflect the manufacturer's sense of responsibility and professionalism.
By comprehensively evaluating the above indicators, the overall performance and quality of the roll film horizontal packaging machine can be accurately assessed. If conditions permit, one can conduct on-site inspections of the manufacturer, personally operate or watch demonstration videos, compare various data, refer to industry evaluations and user feedback, and comprehensively understand the overall quality of the equipment.
Union Machinery has been engaged in food machinery customization services since its establishment in 2014, according to customer needs for you to tailor suitable machinery and equipment, for more product information, please refer to: https://www.hnunmachinery.com/Automatic-Packing-Machine/Automatic-Horizontal-Packaging-Machine/;Our expertise and advantages will bring you more opportunities and development space.
For personalized, industry-tailored advice and to explore state-of-the-art solutions, please don't hesitate to contact us at info@unmachinery.com
The following is other knowledge related to the Horizontal packaging machine that I have summarized based on long-term work experience, for your reference. I hope it will be helpful to you.
1.What is the horizontal bag making packer?
2.What is a premade bag horizontal packaging machine?
3.What are the common faults of the roll film horizontal packaging machine?
4.How to choose between horizontal packaging machine and vertical packaging machine?
5.What factors should be considered when purchasing a roll film stand up pouch packaging machine?
6.How to choose between roll film packaging machine and premade bag packaging machine?