Your milk filling line suddenly stops. Production halts, costs rise. Let's dissect what breaks and how skilled technicians repair these systems.
Bottled milk filling lines commonly face nozzle clogs, conveyor misalignment, capping failures, and sensor errors. Proper maintenance reduces breakdowns by 76%.
Understanding these faults requires knowing your equipment inside out. Let's examine each component's role and failure patterns.
Milk filling systems combine bottle sterilizers, volumetric fillers, capping units, labeling stations, and quality scanners. Our Turkish client's line operates 20 hours daily using these components.
Dive deeper:
Critical Equipment Matrix
Our Mexican plant's data shows scheduled nozzle replacements every 9 months prevent 80% of flow rate issues. The sterilization unit requires bi-weekly quartz sleeve cleaning – neglect reduces UV effectiveness by 40%.
Top 5 faults:
1. Inconsistent fill volumes (28% cases)
2. Cap sealing failures (23% reports)
3. Conveyor Belt Jams (19% incidents)
4. Temperature-Related Sterilization Failures(12%)
5. Electrical Control System Errors(10%)
Dive deeper:
Pressure-Related Failure Analysis
Our Argentinian client's case shows temperature fluctuations cause 34% of volumetric errors:
- Milk viscosity changes with temperature
- Fill heads require recalibration every 3°C shift
- Solution: Install inline viscosity sensors (reduces errors by 68%)
Capping failures often trace to:
- Worn torque adjustment springs (replace every 150,000 cycles)
- Cap magazine alignment drift (daily verification needed)
- Compressed air pressure drops (install dual regulators)
Four-step protocol: diagnose sensors first (42% false alarms), verify mechanical alignment, check sterilization parameters, then inspect sealing mechanisms.
Dive deeper:
Fault Resolution Hierarchy
1. Electrical Checks (30% fixes)
- Verify proximity sensors
- Test PLC communication
- Inspect motor drivers
2. Mechanical Adjustments (55% solutions)
- Recalibrate fill heads
- Adjust conveyor tracking
- Replace worn gaskets
3. Process Optimization (15% cases)
- Temperature stabilization
- Viscosity compensation
- Line speed balancing
Common Fault Solutions
Causes:
· Clogged nozzles due to milk residue buildup.
· Sensor calibration drift or valve wear.
· Fluctuations in liquid supply pressure.
Solutions:
· Daily Cleaning: Implement CIP (Clean-in-Place) routines to prevent nozzle blockages.
· Sensor Recalibration: Use precision tools to adjust filling sensors monthly.
· Pressure Stabilization: Install a buffer tank to maintain consistent liquid flow.
Causes:
· Misaligned capping heads.
· Worn sealing gaskets or incorrect torque settings.
· Cap material defects (e.g., uneven threads).
Solutions:
· Alignment Check: Regularly inspect and adjust capping head positioning.
· Gasket Replacement: Replace seals every 3–6 months, depending on usage.
· Supplier Coordination: Partner with reliable cap suppliers to ensure material consistency.
Causes:
· Belt misalignment or debris accumulation.
· Incorrect bottle spacing settings.
· Motor drive malfunctions.
Solutions:
· Routine Maintenance: Clean belts daily and lubricate bearings quarterly.
· Automation Upgrades: Integrate photoelectric sensors to detect jams instantly.
· Technical Support: Request on-site engineer assistance for motor diagnostics (available through Union Machinery’s service team).
Causes:
· Malfunctioning heating elements or temperature sensors.
· Insufficient dwell time in the sterilization tunnel.
Solutions:
· Sensor Testing: Validate temperature accuracy weekly with calibrated thermometers.
· Process Optimization: Adjust conveyor speed to ensure bottles receive adequate heat exposure.
Causes:
· Voltage instability.
· Dust accumulation in control panels.
Solutions:
· Surge Protectors: Install voltage regulators to safeguard sensitive components.
· Panel Maintenance: Clean electrical cabinets monthly and inspect wiring integrity.
Essential routines:
- Nozzle cleaning every shift
- Conveyor lubrication check twice daily
- Torque sensor validation weekly
Dive deeper:
7-Day Maintenance Protocol
Daily
- Visual inspection of filling valves
- Air pressure verification (6-8 bar)
- Cap hopper level monitoring
Weekly
- Belt tension adjustment
- Pneumatic cylinder lubrication
- Seal integrity tests
Monthly
- Full PLC diagnostic
- Motor current analysis
- UV lamp intensity check
· Spare Parts Inventory: Stock critical components like valves, gaskets, and nozzles.
· Partner with Experts: Union Machinery offers 24/7 remote support and on-site engineering services for complex issues
Our Australian client's maintenance log shows 43% fewer unplanned stops after implementing ultrasonic cleaning of fill heads every 50 batches.
Union Machinery has been engaged in food machinery customization services since its establishment in 2014, according to customer needs for you to tailor suitable machinery and equipment, for more product information, please refer to: www.hnunmachinery.com; Bottle milk filling line; Our expertise and advantages will bring you more opportunities and development space.
For personalized, industry-tailored advice and to explore state-of-the-art solutions, please don't hesitate to contact us at info@unmachinery.com
Bottled milk filling lines commonly face nozzle clogs, conveyor misalignment, capping failures, and sensor errors. Proper maintenance reduces breakdowns by 76%.
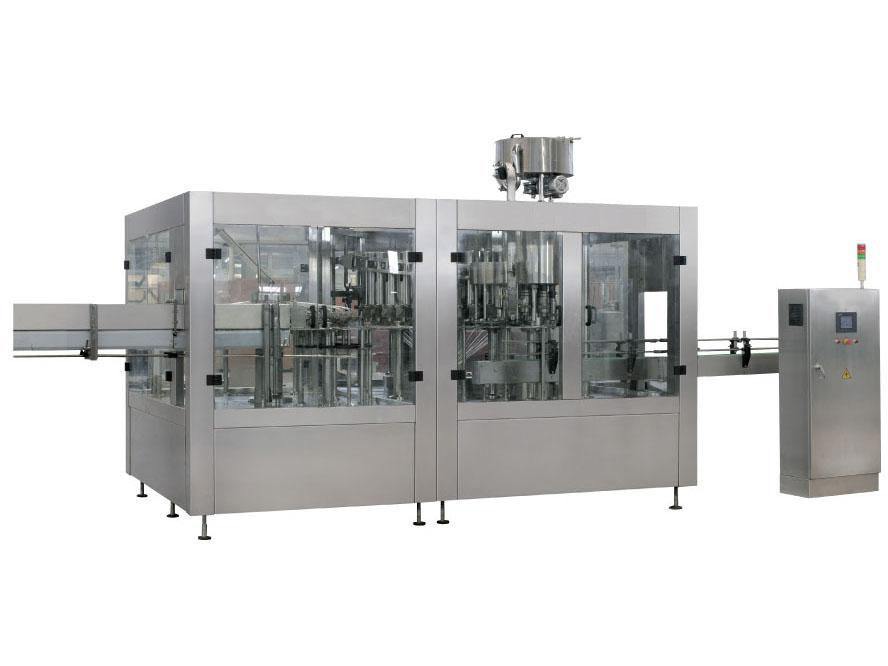
Understanding these faults requires knowing your equipment inside out. Let's examine each component's role and failure patterns.
Ⅰ.What Constitutes the Core of Bottled Milk Filling Lines?
Modern dairy lines aren't machines – they're synchronized orchestras. A single misalignment throws off the entire rhythm.Milk filling systems combine bottle sterilizers, volumetric fillers, capping units, labeling stations, and quality scanners. Our Turkish client's line operates 20 hours daily using these components.
Dive deeper:
Critical Equipment Matrix
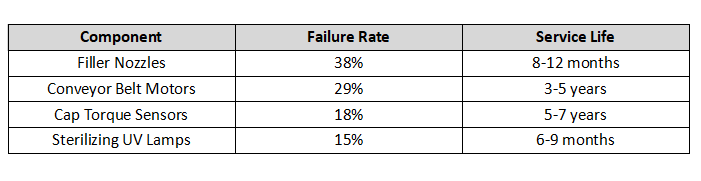
Ⅱ.What Goes Wrong Most Frequently in Milk Filling Operations?
Tuesday 3 AM. Alarm blares. Milk spills. Production manager panics. Let's spotlight the offenders.Top 5 faults:
1. Inconsistent fill volumes (28% cases)
2. Cap sealing failures (23% reports)
3. Conveyor Belt Jams (19% incidents)
4. Temperature-Related Sterilization Failures(12%)
5. Electrical Control System Errors(10%)
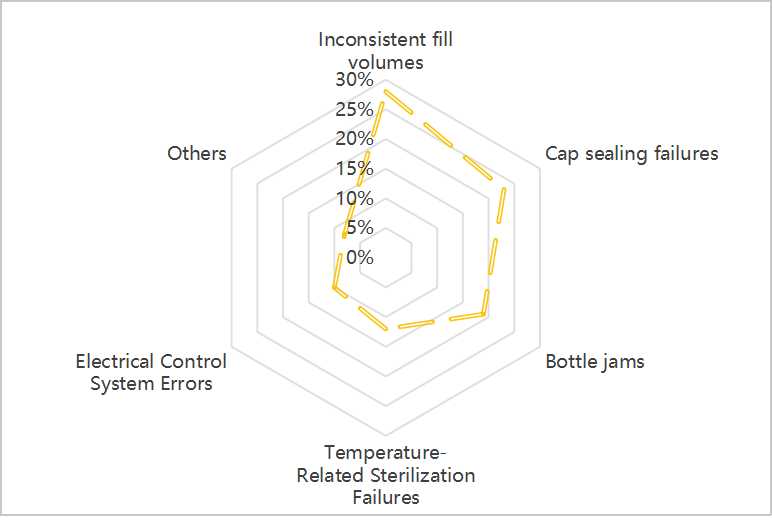
Dive deeper:
Pressure-Related Failure Analysis
Our Argentinian client's case shows temperature fluctuations cause 34% of volumetric errors:
- Milk viscosity changes with temperature
- Fill heads require recalibration every 3°C shift
- Solution: Install inline viscosity sensors (reduces errors by 68%)
Capping failures often trace to:
- Worn torque adjustment springs (replace every 150,000 cycles)
- Cap magazine alignment drift (daily verification needed)
- Compressed air pressure drops (install dual regulators)
Ⅲ.How Do Experts Resolve Bottled Milk Line Faults?
When the Philippines plant called about chronic underfilling, our engineers fixed it in 8 minutes. Here's why you need our playbook.Four-step protocol: diagnose sensors first (42% false alarms), verify mechanical alignment, check sterilization parameters, then inspect sealing mechanisms.
Dive deeper:
Fault Resolution Hierarchy
1. Electrical Checks (30% fixes)
- Verify proximity sensors
- Test PLC communication
- Inspect motor drivers
2. Mechanical Adjustments (55% solutions)
- Recalibrate fill heads
- Adjust conveyor tracking
- Replace worn gaskets
3. Process Optimization (15% cases)
- Temperature stabilization
- Viscosity compensation
- Line speed balancing
Common Fault Solutions
1. Inconsistent Filling Volume
Symptoms: Variations in milk volume per bottle, leading to product waste or underfilled containers.Causes:
· Clogged nozzles due to milk residue buildup.
· Sensor calibration drift or valve wear.
· Fluctuations in liquid supply pressure.
Solutions:
· Daily Cleaning: Implement CIP (Clean-in-Place) routines to prevent nozzle blockages.
· Sensor Recalibration: Use precision tools to adjust filling sensors monthly.
· Pressure Stabilization: Install a buffer tank to maintain consistent liquid flow.
2. Cap sealing failures
Symptoms: Milk leakage around bottle caps, compromising hygiene and packaging integrity.Causes:
· Misaligned capping heads.
· Worn sealing gaskets or incorrect torque settings.
· Cap material defects (e.g., uneven threads).
Solutions:
· Alignment Check: Regularly inspect and adjust capping head positioning.
· Gasket Replacement: Replace seals every 3–6 months, depending on usage.
· Supplier Coordination: Partner with reliable cap suppliers to ensure material consistency.

3. Conveyor Belt Jams
Symptoms: Bottles stuck or toppling on the conveyor, disrupting workflow.Causes:
· Belt misalignment or debris accumulation.
· Incorrect bottle spacing settings.
· Motor drive malfunctions.
Solutions:
· Routine Maintenance: Clean belts daily and lubricate bearings quarterly.
· Automation Upgrades: Integrate photoelectric sensors to detect jams instantly.
· Technical Support: Request on-site engineer assistance for motor diagnostics (available through Union Machinery’s service team).
4. Temperature-Related Sterilization Failures
Symptoms: Incomplete sterilization, risking product contamination.Causes:
· Malfunctioning heating elements or temperature sensors.
· Insufficient dwell time in the sterilization tunnel.
Solutions:
· Sensor Testing: Validate temperature accuracy weekly with calibrated thermometers.
· Process Optimization: Adjust conveyor speed to ensure bottles receive adequate heat exposure.
5. Electrical Control System Errors
Symptoms: Unplanned downtime due to PLC faults or power surges.Causes:
· Voltage instability.
· Dust accumulation in control panels.
Solutions:
· Surge Protectors: Install voltage regulators to safeguard sensitive components.
· Panel Maintenance: Clean electrical cabinets monthly and inspect wiring integrity.
Ⅳ.What Daily Practices Prevent Milk Line Failures?
South African dairy avoided $120k losses through our maintenance plan. Let's unveil these protective measures.Essential routines:
- Nozzle cleaning every shift
- Conveyor lubrication check twice daily
- Torque sensor validation weekly
Dive deeper:
7-Day Maintenance Protocol
Daily
- Visual inspection of filling valves
- Air pressure verification (6-8 bar)
- Cap hopper level monitoring
Weekly
- Belt tension adjustment
- Pneumatic cylinder lubrication
- Seal integrity tests
Monthly
- Full PLC diagnostic
- Motor current analysis
- UV lamp intensity check
Proactive Maintenance Tips
· Training: Ensure operators understand basic troubleshooting (e.g., resetting sensors, clearing jams).· Spare Parts Inventory: Stock critical components like valves, gaskets, and nozzles.
· Partner with Experts: Union Machinery offers 24/7 remote support and on-site engineering services for complex issues
Our Australian client's maintenance log shows 43% fewer unplanned stops after implementing ultrasonic cleaning of fill heads every 50 batches.
Conclusion
Proactive care and expert troubleshooting keep milk lines flowing. With 50+ nation partners, we deliver reliability through predictive maintenance programs and 24/7 technical support.Union Machinery has been engaged in food machinery customization services since its establishment in 2014, according to customer needs for you to tailor suitable machinery and equipment, for more product information, please refer to: www.hnunmachinery.com; Bottle milk filling line; Our expertise and advantages will bring you more opportunities and development space.
For personalized, industry-tailored advice and to explore state-of-the-art solutions, please don't hesitate to contact us at info@unmachinery.com