How to quickly solve problems and improve production efficiency?
Have you lost orders due to frequent downtime of the packaging machine? Is the production line card delay causing delivery delay? Don't let the malfunction drag down your profits! We have summarized 5 common problems and solutions to help you quickly resume production.
This article provides five rapid diagnostic methods for high-frequency faults in cup finger biscuit packaging machines, covering core issues such as mechanical adjustment, sensor calibration, and material adaptation. By optimizing operational processes and preventive maintenance, you can reduce downtime by over 60%.
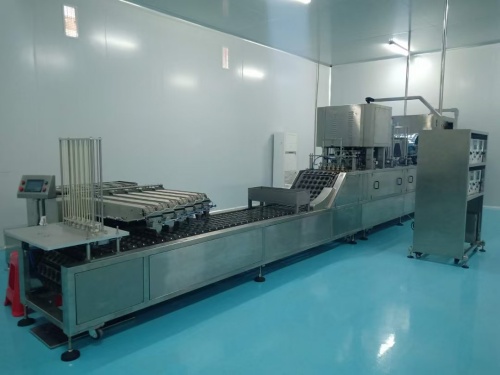
1. Error in the quantity of biscuits filled
Problem phenomenon: The quantity of biscuits placed is inconsistent and does not meet the product consistency requirements.Causes:
- Feed channel issue: The channel is too wide or too narrow, causing the biscuits to jam, stack, or scatter during transportation, affecting counting accuracy.
- Counting sensor malfunction: The surface of the photoelectric sensor is covered with dust, contaminated with grease, or the installation position is offset, which makes it impossible to accurately detect the number of biscuits.
- Inconsistent biscuits sizes: When there are significant differences in the length and thickness of finger biscuits, the sensor may mistake multiple cookies for a single one or miss them due to overlapping.
- Inadequate equipment debugging: The counting system was not calibrated before startup, or mechanical parameters (such as conveyor belt speed and vibration frequency) were not adjusted according to the characteristics of the batch of biscuits.
- Insufficient cleaning and maintenance: Residual biscuit crumbs or grease on the feeding channel and sensor surface, which were not cleaned in a timely manner, resulting in detection failure.
Solutions:
- Adjust the feeding channel parameters: Design the channel width accurately based on the size of the biscuits (usually 1-2mm larger than the biscuit diameter), install guide plates or partition devices to ensure that biscuits are transported in an orderly manner in a single row.
- Cleaning and calibrating sensors: Wipe the surface of the photoelectric sensor with anhydrous alcohol daily to ensure that the detection light path is unobstructed; Regularly calibrate sensor sensitivity with standard sized biscuits.
- Standardize the production process of biscuits: Require upstream production lines to control the size tolerance of biscuits (such as length error ≤± 2mm) and reduce the proportion of irregular biscuits (recommended to be controlled within 5%).
- Standardized equipment debugging process: Before starting up, perform an "empty machine test run+physical calibration": first run the machine empty for 5 minutes to check the transmission stability, and then test the counting accuracy with 50-100 biscuits (required to be ≥ 99.5%).
- Establish a regular maintenance ledger: Develop a "Packaging Machine Maintenance Plan", clean the feeding channel weekly, check the tightness of sensor brackets monthly, lubricate mechanical transmission components quarterly, and record maintenance results.
2. Incomplete sealing or insufficient heat - sealing strength
Problem phenomenon: Leakage or delamination occurs at the sealing area, leading to product leakage, deterioration, or a shortened shelf life, which affects product quality..Causes:
- Incorrect temperature: Too low a sealing temperature will result in an insecure seal, while too high a temperature may scorch the bag mouth.
- Mismatched sealing pressure: Too little pressure will cause incomplete sealing, and too much pressure will damage the material and cause air leakage.
- Sealing mold damage: After long - term use, the sealing mold may wear, resulting in uneven sealing.
- Sealing material quality problem: Unqualified or mismatched sealing materials, material changes, or contamination may lead to poor sealing.
- Aging of heating elements: Aging of heating elements affects the heating effect.
Solutions:
- Preset multiple groups of parameters according to the film characteristics (such as PE/PP/Aluminum composite film) and switch the formula with one key.
- Use dual - channel temperature monitoring technology to adjust the temperature of the heat - sealing head in real - time.
- Equip with a self - cleaning device to avoid residues affecting the sealing quality.
- Adjust the sealing temperature to ensure it is within an appropriate range.
- Regularly check and replace the sealing mold to ensure it is in good working condition.
- Select high - quality sealing materials and choose appropriate materials according to the product characteristics.
3. Conveyor belt jamming or positioning deviation
Problem phenomenon: The cups or bowls are not accurately positioned, resulting in misalignment during filling or sealing and an increase in the rejection rate.Causes:
- Transmission jamming: Insufficient lubrication of mechanical transmission parts.
- Sensor problem: Insufficient sensitivity of the photoelectric sensor.
- Equipment failure: Loosening of parts due to equipment vibration.
Solutions:
- Use maintenance - free self - lubricating guide rails to reduce manual intervention.
- Upgrade to a visual positioning system (optional) to intelligently identify the container position and perform dynamic correction.
- Adopt a full - body anti - vibration design to adapt to high - speed continuous production.
5. Excessive Vibration or Noise
Problem performance: The equipment generates abnormal vibration or noise during operation, which may lead to instability of the production line and even affect the operation of other equipment.Causes:
- Loose mechanical parts: After long - term use, some screws or connectors of the equipment may become loose, resulting in vibration or noise.
- Poor lubrication: Lack of proper lubrication for mechanical moving parts may increase friction and generate noise.
- Unbalanced load: Uneven or unstable equipment load can also cause vibration and noise.
Solutions:
- Regularly check and tighten all parts of the equipment to ensure they are firmly fixed.
- Ensure that all moving parts are properly lubricated to reduce friction.
- Check the equipment load to ensure it is evenly distributed and avoid vibration caused by unbalanced operation.
6. Frequent Production Line Shutdowns
Problem performance: The equipment shuts down frequently, affecting production efficiency and causing significant production losses.Causes:
- Electrical failure: Malfunctions in the electrical control system may cause the equipment to suddenly shut down, especially due to unstable power supply or aging electrical components.
- Transmission system failure: Problems with the transmission belt, chain, or motor may prevent the equipment from operating normally.
- Sensor failure: Malfunctioning sensors may cause the equipment to fail to accurately identify materials or positions, triggering the shutdown protection.
Solutions:
- Regularly check electrical components to ensure the normal operation of the power supply and control system.
- Check all parts of the transmission system to ensure they are not worn or loose.
- Regularly calibrate sensors to ensure their accurate working status.
Union Machinery has been engaged in food machinery customization services since its establishment in 2014, according to customer needs for you to tailor suitable machinery and equipment, for more product information, please refer to: https://www.hnunmachinery.com/Automatic-Cups-Filling-and-Sealing-Machine/More video information see view: cups-filling-and-foil-sealing-machine cups-filling-and-sealing-machine coffee-capsule-filling-and-sealing-machine;Our expertise and advantages will bring you more opportunities and development space.
For personalized, industry-tailored advice and to explore state-of-the-art solutions, please don't hesitate to contact us at info@unmachinery.com
The following is other knowledge related to the cups filling and sealing machine that I have summarized based on long-term work experience, for your reference. I hope it will be helpful to you.
1.What is the cup filling machine?
2.How to Choose the Perfect Jelly Filling and Sealing Machine?
3.How did jelly get into your mouth?