Common Jelly Filling and Sealing Machine Failures & Expert Solutions – Smarter, More Reliable Production
In the global food processing industry, jelly filling and sealing machines are critical for enhancing production efficiency and ensuring product consistency, widely used in packaging jelly, juice, yogurt, and similar products. However, even high-performance automated equipment may experience temporary failures due to operational, maintenance, or environmental factors. Understanding common issues and solutions not only minimizes downtime but also helps you select a truly reliable, technologically advanced filling and sealing machine.Below are the eight most common failures and professional solutions for jelly filling and sealing machines, combined with the core advantages of Union Machinery equipment, to help you achieve efficient, worry-free production.
1. Uneven filling volume or accuracy deviation
Problem phenomenon: Fluctuations in jelly filling volume lead to inconsistent product specifications, impacting quality and cost control.Causes:
- Filling valve failure: Foreign objects clogging or component wear (such as pump valves and pistons) inside the filling valve may lead to inaccurate filling volume.
- Air pressure problem: Insufficient air pressure in the equipment can affect the liquid flow, causing uneven filling.
- Liquid viscosity change: The viscosity change of jelly liquid can also affect the filling volume, especially under high - or low - temperature conditions.
- Sensor failure: The sensitivity of the sensor decreases.
Solutions:
- Regularly clean the feeding pipeline to ensure material fluidity.
- Regularly clean the filling valve to ensure there are no foreign objects or impurities clogging it.
- Adopt dynamic calibration technology (such as an intelligent weighing feedback system) to monitor and automatically adjust the filling volume in real - time.
- Use a modular design for key components to quickly replace vulnerable parts and reduce maintenance time.
- Check the air pressure system to ensure the air pressure is stable and meets the equipment requirements.
- Adjust the parameters of the filling valve to adapt to different liquid viscosities.
Our Advantage:
Union Machinery's filling and sealing machine is equipped with a high - precision servo drive system, with an error rate below ±0.5%, ideal for high-viscosity materials like jelly and pudding, ensuring consistent product quality.
2. Incomplete sealing or insufficient heat - sealing strength
Problem phenomenon: Leakage or delamination occurs at the sealing area, leading to product leakage, deterioration, or a shortened shelf life, which affects product quality.. Causes:
- Incorrect temperature: Too low a sealing temperature will result in an insecure seal, while too high a temperature may scorch the bag mouth.
- Mismatched sealing pressure: Too little pressure will cause incomplete sealing, and too much pressure will damage the material and cause air leakage.
- Sealing mold damage: After long - term use, the sealing mold may wear, resulting in uneven sealing.
- Sealing material quality problem: Unqualified or mismatched sealing materials, material changes, or contamination may lead to poor sealing.
- Aging of heating elements: Aging of heating elements affects the heating effect.
Solutions:
- Preset multiple groups of parameters according to the film characteristics (such as PE/PP/Aluminum composite film) and switch the formula with one key.
- Use dual - channel temperature monitoring technology to adjust the temperature of the heat - sealing head in real - time.
- Equip with a self - cleaning device to avoid residues affecting the sealing quality.
- Adjust the sealing temperature to ensure it is within an appropriate range.
- Regularly check and replace the sealing mold to ensure it is in good working condition.
- Select high - quality sealing materials and choose appropriate materials according to the product characteristics.
Our Advantage:
Union Machinery's equipment uses a new heat - sealing technology to precisely control energy output, improving the sealing effect by 30% while reducing energy consumption.
3. Conveyor belt jamming or positioning deviation
Problem phenomenon: The cups or bowls are not accurately positioned, resulting in misalignment during filling or sealing and an increase in the rejection rate. Causes:
- Transmission jamming: Insufficient lubrication of mechanical transmission parts.
- Sensor problem: Insufficient sensitivity of the photoelectric sensor.
- Equipment failure: Loosening of parts due to equipment vibration.
Solutions:
- Use maintenance - free self - lubricating guide rails to reduce manual intervention.
- Upgrade to a visual positioning system (optional) to intelligently identify the container position and perform dynamic correction.
- Adopt a full - body anti - vibration design to adapt to high - speed continuous production.
Our Advantage:
Union Machinery's equipment supports a stable operating speed of up to 200 packs per minute, paired with an industrial - grade servo motor, with a positioning accuracy of ±0.1mm.
4. Contamination or Residuals in Hard-to-Clean Areas
Problem phenomenon: Jelly residues remain inside the equipment, breeding bacteria or contaminating the next batch of products. Causes:
- Incomplete cleaning: The complex equipment structure makes manual cleaning difficult.
- Lack of cleaning function: Incomplete coverage of the CIP (Clean - in - Place) system.
Solutions:
- Adopt an open and detachable structural design, allowing all contact parts to be flexibly disassembled.
- Provide a fully automatic CIP cleaning module to complete the in - depth cleaning of pipes and filling heads with one key.
Our Advantage:
Our equipment conforms to the national health standards. Through a corner - free rounded design and food - grade stainless - steel material, production safety is guaranteed.
5. Excessive Vibration or Noise
Problem performance: The equipment generates abnormal vibration or noise during operation, which may lead to instability of the production line and even affect the operation of other equipment. Causes:
- Loose mechanical parts: After long - term use, some screws or connectors of the equipment may become loose, resulting in vibration or noise.
- Poor lubrication: Lack of proper lubrication for mechanical moving parts may increase friction and generate noise.
- Unbalanced load: Uneven or unstable equipment load can also cause vibration and noise.
Solutions:
- Regularly check and tighten all parts of the equipment to ensure they are firmly fixed.
- Ensure that all moving parts are properly lubricated to reduce friction.
- Check the equipment load to ensure it is evenly distributed and avoid vibration caused by unbalanced operation.
Our advantages:
Our equipment uses advanced technology and processes, paying attention to the precision machining and installation of every component to ensure the stability and working effect of the equipment.
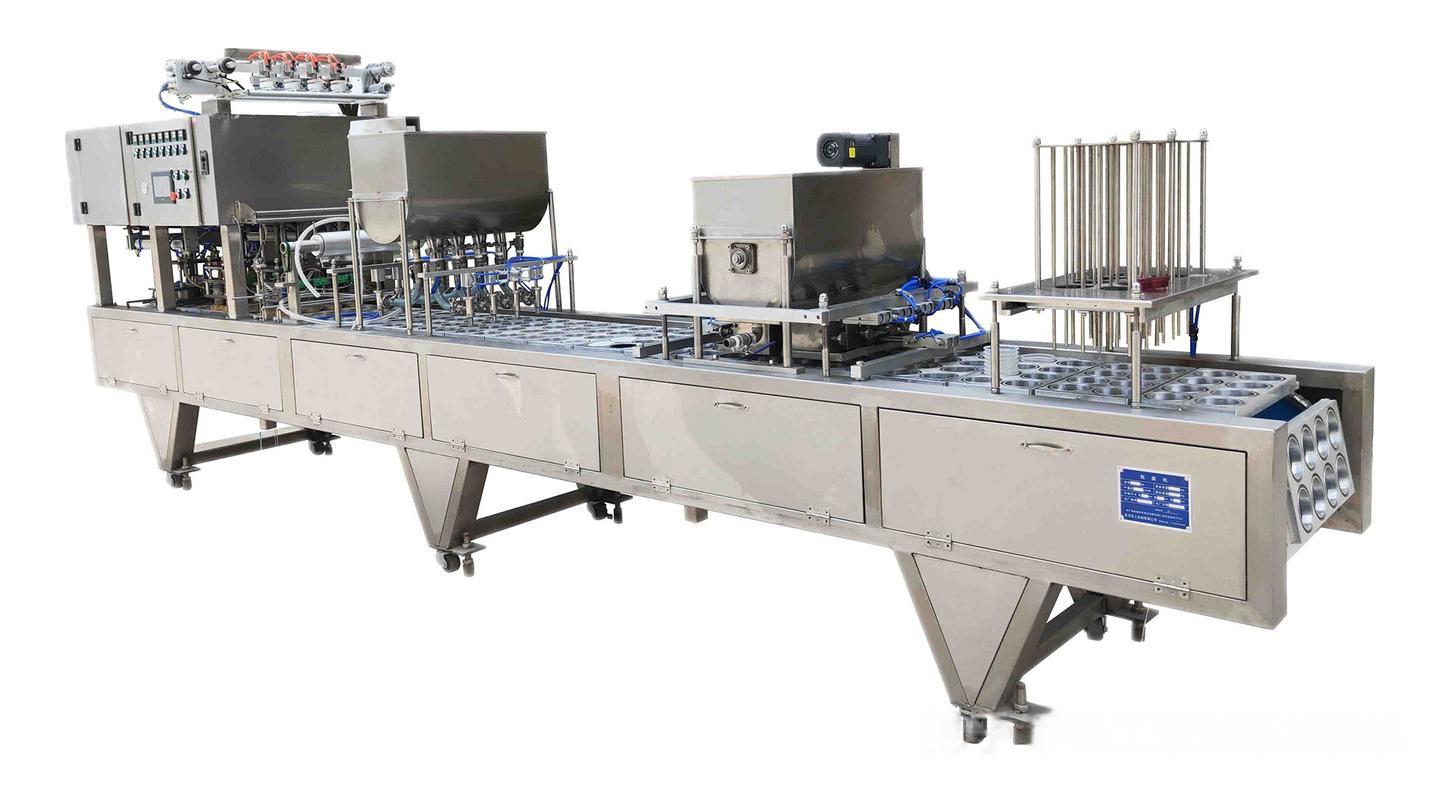
6. Frequent Production Line Shutdowns
Problem performance: The equipment shuts down frequently, affecting production efficiency and causing significant production losses.Causes:
- Electrical failure: Malfunctions in the electrical control system may cause the equipment to suddenly shut down, especially due to unstable power supply or aging electrical components.
- Transmission system failure: Problems with the transmission belt, chain, or motor may prevent the equipment from operating normally.
- Sensor failure: Malfunctioning sensors may cause the equipment to fail to accurately identify materials or positions, triggering the shutdown protection.
Solutions:
- Regularly check electrical components to ensure the normal operation of the power supply and control system.
- Check all parts of the transmission system to ensure they are not worn or loose.
- Regularly calibrate sensors to ensure their accurate working status.
Our advantages:
Our equipment uses advanced control systems and high - precision sensors. After precision machining and strict quality control, all products are rigorously tested before leaving the factory to ensure the stability of the machine.
7. Poor Product Appearance
Problem performance: The product appearance shows damage, leakage, or uneven sealing, which affects the market acceptance of the product. Causes:
- Packaging bag quality problem: If the packaging bag material is unqualified or over - stretched, it may lead to uneven sealing and affect the appearance.
- High filling temperature: High - temperature filling may cause the jelly to overflow or the bag to seal loosely.
- Excessive equipment speed: When the equipment runs too fast, it may cause instability during the filling and sealing process, thus affecting the product appearance.
Solutions:
- Use packaging materials that meet the standards and ensure consistent bag quality.
- Adjust the filling temperature to avoid the impact of too high or too low temperatures on the jelly.
- Adjust the equipment operating speed according to production needs to ensure a smooth filling and sealing process.
Our advantages:
Union Machinery's jelly filling and sealing machine has a high degree of automation, reducing manual operation. It can achieve automated filling, sealing, and adjustment processes, with real - time monitoring to ensure product quality.
8. Complex human - machine interaction and time - consuming fault diagnosis
Problem phenomenon: The operation interface is cumbersome, fault codes are difficult to interpret, and on - site maintenance by engineers is often required. Solutions:
- Intelligent touch screen: The graphical interface supports multi - language switching, allowing operators to quickly adjust parameters.
- AI early - warning system: Real - time monitoring of the equipment status to provide early warnings for potential faults (such as motor overload and temperature abnormalities).
- Remote technical support: Through the Internet of Things module, engineers can diagnose and guide repairs online.
Our advantages:
Union Machinery is committed to creating "zero - learning - cost" equipment, providing multi - language operation manuals and 24/7 global technical support to ensure worry - free production for customers.
Why Choose Union Machinery Jelly Filling & Sealing Machines?
✅ High adaptability: Compatible with various containers (plastic cups, glass bottles, stand - up pouches) and viscous materials. ✅ Energy - saving design: Reduces energy consumption by 40% compared with traditional equipment, in line with the trend of green production.
✅ Fast delivery: Standardized modules + flexible customization, shortening the delivery cycle by 30%.
✅ Global service network: Verified by customers in more than 50 countries, with a 48 - hour rapid response for spare parts.
Transform Efficiency into Your Competitive Edge!
Whether upgrading existing lines or launching new facilities, Union Machinery’s jelly filling and sealing machines deliver unmatched stability, intelligence, and post-sales service to help you dominate the market.Take Action Now to Get Your Customized Solution!
Your Success Drives Our Innovation.
Union Machinery – Your Global Partner in Intelligent Packaging Solutions
Union Machinery has been engaged in food machinery customization services since its establishment in 2014, according to customer needs for you to tailor suitable machinery and equipment, for more product information, please refer to: https://www.hnunmachinery.com/Automatic-Cups-Filling-and-Sealing-Machine/More video information see view: cups-filling-and-foil-sealing-machine cups-filling-and-sealing-machine coffee-capsule-filling-and-sealing-machine;Our expertise and advantages will bring you more opportunities and development space.
For personalized, industry-tailored advice and to explore state-of-the-art solutions, please don't hesitate to contact us at info@unmachinery.com
The following is other knowledge related to the cups filling and sealing machine that I have summarized based on long-term work experience, for your reference. I hope it will be helpful to you.
1.What is the cup filling machine?
2.How to Choose the Perfect Jelly Filling and Sealing Machine?
3.How did jelly get into your mouth?
4.How much does a jelly filling production line cost?
5.What is a cup yogurt filling and sealing machine?
6.How much is the cup yogurt filling and sealing machine?